Polycarbonate
Polycarbonate is an amorphous thermoplastic that is naturally transparent, though it can also be found in a variety of colors. This material allows for the transmission of light nearly with the same capacity as glass. Its density is about 1.2 gr/cm3, and it has a melting point of 300 . Polycarbonate granules are used for the production of various items, especially where impact resistance and transparency are important. For example, they are used in bulletproof glass, personal computers, plastic lenses in eyewear, medical devices, automotive parts, protective gear, greenhouses, digital discs, and outdoor lighting fixtures. One major use of this material is in molding, due to its resistance to thermal changes, making it widely applicable. Polycarbonate granules can be easily shaped by heat without cracking or breaking. You can create small angles in this polymer without using heat. These granules come in various sizes and are highly resistant to UV rays and impact. All these features have made polycarbonate widely used in different industries. Unlike thermosets, this polymer softens with heat. One notable characteristic of this sheet is that it can be heated up to its melting point and then cooled down again without significant degradation. Instead of burning, polycarbonate turns into liquid, allowing it to be easily injected or recycled. Exporting Polycarbonate to various countries with the best price has been one of the achievements of Petro Nour Mehr Company in recent years. For more accurate information regarding prices or purchasing the product, it is better to contact the sales department of Petro Nour Mehr Company.
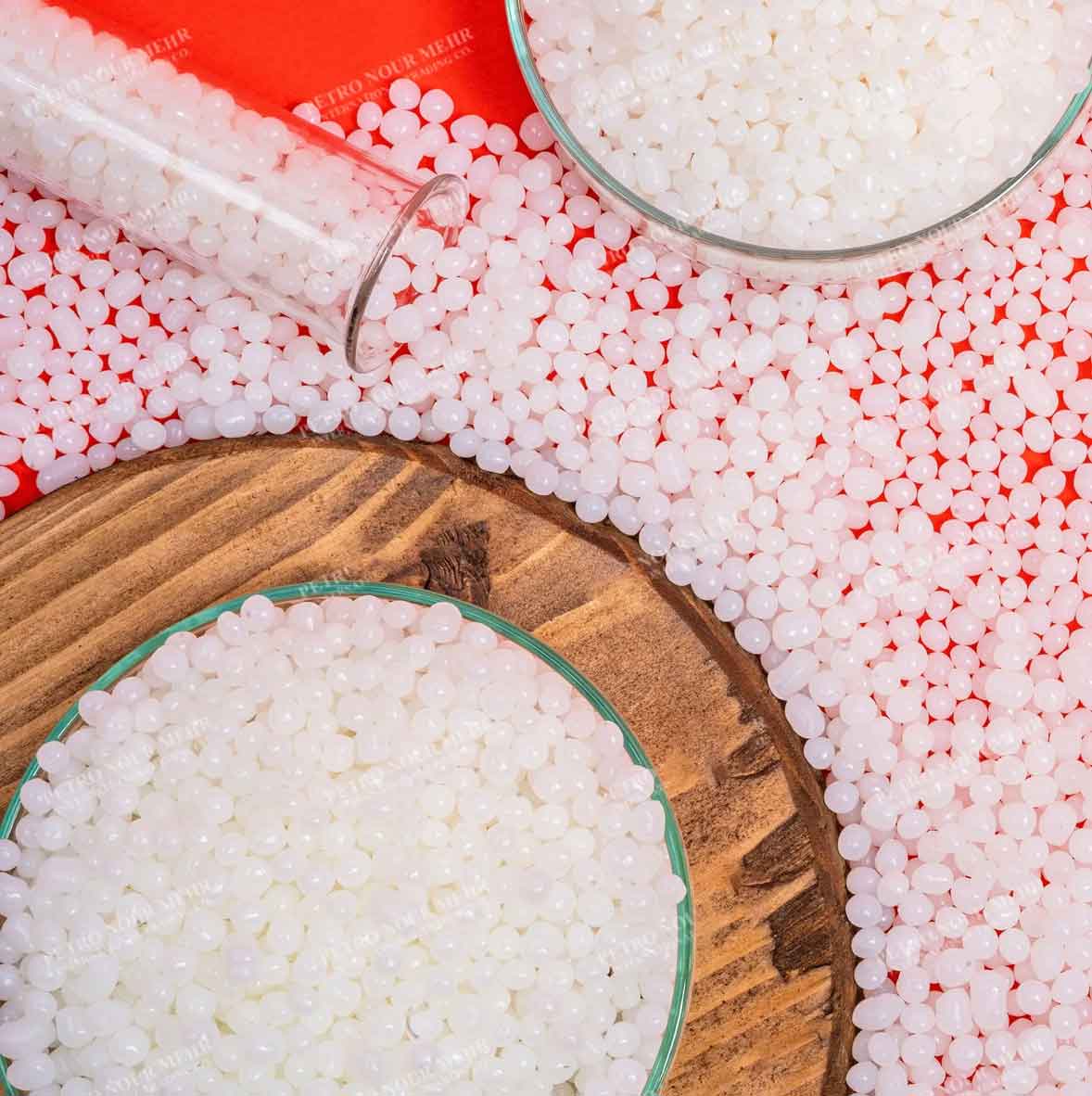
Rubber Manufacturers in Iran
In the petrochemical industry of Iran, several companies and production units are engaged in the production of Rubber. These companies include:
- Shazand Arak Petrochemical Company
- Takht-e-Jamshid Petrochemical Company
These units are among the largest Rubber producers in Iran and play a significant role in supplying domestic needs and exporting this material to global markets.
Rubber Manufacturers Worldwide
Throughout the world, the polymer and rubber industry are recognized as an important sector of the chemical industry, with numerous manufacturers active in this field. Some of the largest polymer and rubber producers in the Americas include:
- DuPont: This company is one of the largest polymer and rubber manufacturers in the world, and its products are used in many industries including automotive, electronics, packaging, and consumer goods.
- LyondellBasell: A large polymer company producing a variety of products including rubbers, polyethylene, polypropylene, polystyrene, and more. Its products are distributed in various global markets.
- Innova: Known as one of the largest polymer producers in North America, Innova’s products are widely used in industries such as automotive, electronics, packaging, and more.
These manufacturers are just a few examples of the largest Rubber producers globally, and the Rubber industry in these regions benefits from the efforts of many other companies as well.
Applications of Rubber
Rubber is a versatile material used across various industries due to its elasticity, durability, and resistance to environmental conditions. Key applications include:
- Automotive: Tires, seals, hoses, and belts.
- Construction: Sealants, flooring, and vibration dampening.
- Healthcare: Medical gloves, tubing, and surgical products.
- Consumer Goods: Footwear, household items, and sporting goods.
- Electronics: Insulation, keypads, and protective cases.
- Industrial: Conveyor belts, rubber rollers, and gaskets.
- Aerospace: O-rings, seals, and insulation.
- Marine: Boat fenders, hoses, and seals.
Rubber’s adaptability makes it essential in many applications, with specific types chosen based on the requirements of each use.
Storage Conditions for Rubber
Rubber requires adequate storage conditions to maintain its characteristics and extend its lifespan. Here are the essential guidelines:
- Temperature: Store Rubber in a cool, dry place. Avoid exposure to extreme temperatures (both high and low). Optimal storage temperature is typically between 15-25°C (59-77°F).
- Humidity: Keep Rubber away from moisture. High humidity can affect the material’s properties over time. Store it in an environment with low humidity.
- Light: Avoid prolonged exposure to direct sunlight or UV light, as it can cause degradation and discoloration. Store Rubber in a dark or covered area.
- Oxygen and Ozone: Minimize exposure to oxygen and ozone, as they can cause oxidation and degradation of the material.
- Packaging: Keep Rubbers in its original packaging if possible, or use airtight and moisture-proof containers.
- Stacking: Avoid heavy stacking that might cause deformation. If stacking is necessary, ensure that the weight is evenly distributed.
- Cleanliness: Store Rubber in a clean environment, free from dust, dirt, and other contaminants.
- Avoid Mechanical Stress: Handle this polymer with care to avoid scratches, cuts, or other mechanical damage.
- Chemical Exposure: Keep Rubber away from chemicals, solvents, and other materials that could cause degradation.
By following these storage guidelines, you can ensure that your Rubber remains in good condition for its intended use.
Packaging for Polystyrene
For packaging and exporting polystyrene granules, various methods can be utilized depending on environmental conditions, product needs, and facilitating transportation for export. Below are some common methods for packaging and exporting these polymer granules:
- Packaging in Jumbo Bags: This is a common method for packaging PS granules, where the granules are packed into large bags with varying capacities (usually between 500 to 2000 kilograms). These bags not only protect the product from contamination and moisture but are also suitable for road, sea, and air transport.
- Packaging in Small Bags: In this method, the polymer granules are packed into smaller bags with a capacity of around 25 to 50 kilograms. These bags are used for retail stores and local markets or for small shipments.
- Using Pallets: These polystyrene granules are usually packed on large pallets. This method is used for transportation.
Attention to international packaging standards, labeling, and transportation conditions can influence the choice of appropriate packaging and exporting methods for polystyrene granules. Additionally, it is important to emphasize protecting the product from shocks, moisture, and environmental damage during transportation.
Physical and Chemical Properties of Rubber
Physical Properties
- Particle Size: Typically 0.5 mm to 5 mm.
- Density: Bulk density ranges from 0.4 to 0.6 g/cm³.
- Elasticity: High elasticity, absorbing impacts well.
- Hardness: Shore A hardness typically between 60-80.
- Color: Usually black, though they can be colored.
- Texture: Rough and irregular, aiding in binding.
- Thermal Properties: Low thermal conductivity, good insulation.
Chemical Properties
- Composition: Made of natural or synthetic rubber polymers with fillers like carbon black.
- Chemical Stability: Resistant to many chemicals, but can degrade in strong acids or UV light.
- Oxidation: Susceptible to hardening over time due to oxidation.
- Hydrocarbons: Can absorb oils, leading to softening.
- Decomposition: Decomposes at high temperatures, releasing VOCs.
- Vulcanization: Cross-linked structure that enhances elasticity and durability.
Types of Rubber grades
Rubbers are among the essential elements in chemical compounds and polymer materials, which, due to their wide range of properties and applications, are divided into various types. These divisions include:
- Silicone Rubbers: Silicone rubbers are a category of rubbers derived from silane compounds. These types of rubbers are typically used in silane polymerization processes. Different structures of silicone rubbers can create various improvements in polymer materials, including increased flexibility, corrosion resistance, increased temperature resistance, and improved mechanical properties.
Examples of silicone rubbers include epoxy silicone rubbers, polyester silicone rubbers, and urethane silicone rubbers. These rubbers are used as additives in polymer material formulations to improve desired properties in final products. - Polymer Rubbers: Polymer rubbers are an important and broad category of rubbers made from polymers or containing polymers in their structure. These types of polymers are usually used as the main material or additive in polymer compositions.
They can enhance the mechanical, thermal, electrical, and chemical properties of polymer materials and improve the performance of final products. Examples of polymer rubbers include polyethylene rubbers, polypropylene rubbers, polyamide rubbers, and polystyrene rubbers. These materials are used as reinforcing agents, flame retardants, plasticizers, and modifiers in polymer material production and formulation processes. - Acrylic Rubbers: Acrylic rubbers are among the important types of these polymer materials synthesized from acrylic and methacrylic monomers. Due to their special properties, acrylic rubbers are used in various industries. Acrylic rubbers are usually used to improve flexibility, water resistance, heat resistance, and corrosion resistance.
These polymer materials are widely used in the paint, resin, waterproofing, adhesive, and lubricant industries. Common examples of acrylic rubbers include acrylic resins, acrylic emulsions, and acrylic polymers. - Sulfur-Modified Rubbers: These polymers are a type of rubbers that contain sulfur groups in their structure. These sulfur groups can be formed from various materials such as thiocyanates, dithiocarbamates, and thioureas. Typically, these rubbers are used to improve specific properties such as corrosion resistance, temperature resistance, and chemical resistance in polymer materials.
They are used to enhance the mechanical and chemical properties of rubbers and plastics, for example, in the automotive and construction industries. These materials can also act as antioxidant and anticorrosive agents, improving product resistance to rust and corrosion. - Specialty Rubbers: These polymer materials are a category of rubbers designed for specific or unique applications. These materials often have special properties that distinguish them from other types of rubbers. For example, thermoplastic rubbers, which can easily change shape with temperature changes, are suitable for use in molding and thermal forming processes.
Additionally, food-grade rubbers, made from non-toxic materials and safe for contact with food, are used in the food industry. Other examples of specialty rubbers include metallic rubbers for creating connections between different materials and rubbers used in the medical industry for making medical instruments and equipment.
Comparison between PBR and SBR
Polybutadiene rubber (PBR) and styrene-butadiene rubber (SBR) are both types of synthetic rubbers widely used in various industries. Here’s a comparison between the two:
Composition:
- PBR: Polybutadiene rubber is a homopolymer derived solely from the polymerization of butadiene monomers.
- SBR: Styrene-butadiene rubber is a copolymer consisting of styrene and butadiene monomers.
Properties:
- PBR: Polybutadiene rubber exhibits high resilience, excellent abrasion resistance, low glass transition temperature (Tg), and good resistance to wear and tear. It is commonly used in tire sidewalls, conveyor belts, and footwear due to its high elasticity.
- SBR: Styrene-butadiene rubber offers good abrasion resistance, excellent tear strength, and high tensile strength. It has better heat resistance and aging properties compared to natural rubber. SBR is often used in tire treads, footwear soles, gaskets, and hoses.
Cost:
- PBR: Polybutadiene rubber tends to be more expensive compared to SBR due to its higher manufacturing costs.
- SBR: Styrene-butadiene rubber is relatively cost-effective and has a lower production cost compared to PBR.
Environmental Impact:
- Both PBR and SBR are synthetic rubbers derived from petrochemical sources, so their environmental impact in terms of production and disposal is similar. However, efforts are being made to develop sustainable alternatives and improve recycling processes for synthetic rubbers to reduce their environmental footprint.
In summary, while both PBR and SBR are synthetic rubbers with excellent properties suitable for various applications, they differ in composition, properties, cost, and specific applications. The choice between PBR and SBR depends on the requirements of the intended application, cost considerations, and performance characteristics needed for the end product.
How to Buy Polyethylene?
- Buy from a reputable and authorized supplier that holds necessary certifications and guarantees quality.
- Compare the prices of these materials in different markets and compare them with the global market price.
- Examine the sales conditions regarding quantity, delivery time, packaging, transportation methods, and payment terms.
- If you intend to import polystyrene from foreign countries, investigate customs and legal regulations and comply with export and import regulations.
- Contact bravopolymer to obtain the most suitable export price based on your conditions.
- After signing the contract, you can place your order.
- Secure and suitable payment methods according to customer preferences are provided by the company.
- Then, the loading stage is completed by selecting and introducing a transport company.
- Necessary documents for customs clearance at the destination city are also provided to customers by bravopolymer.
The largest distributor of polymers in the Middle East

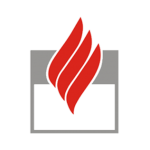

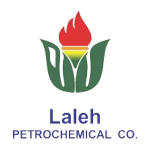
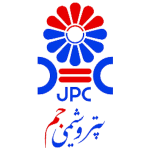
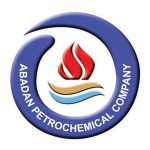
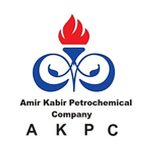
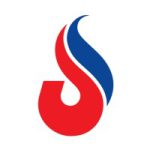
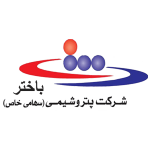
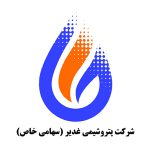
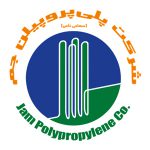
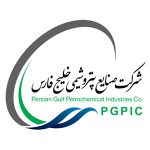
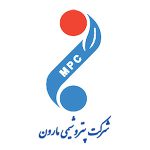
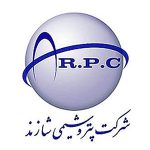
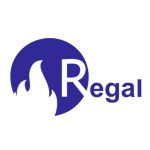
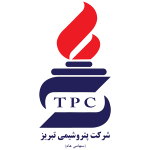
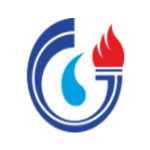