PBR
Polybutadiene rubber (PBR) Polybutadiene rubber (PBR) is a type of synthetic rubber made primarily from polybutadiene as the main material. PBR is widely used in industries such as automotive, industrial rubber, packaging, and construction due to its properties such as flexibility, abrasion resistance, and oxidation resistance. Its relatively low production cost and desirable characteristics have made it a popular choice in many industries. Approximately 70% of polybutadiene production is consumed by the rubber industry, with another 25% used as additives to improve surface properties of plastic compounds like polystyrene and acrylonitrile butadiene. In 2012, PBR was recognized as the fourth most widely used chemical globally. This rubber shares similar properties with natural rubber (NR), isoprene rubber (IR), and styrene-butadiene rubber (SBR). To achieve desired properties, PBR is often blended with other rubbers. For instance, a blend of PBR and SBR is a suitable combination used in modern tire manufacturing, where PBR contributes tear resistance and SBR optimizes rolling friction. To obtain more precise information on Polybutadiene rubber (PBR) prices or product purchases, it is better to contact the Petro Nour Mehr Company’s sales department.
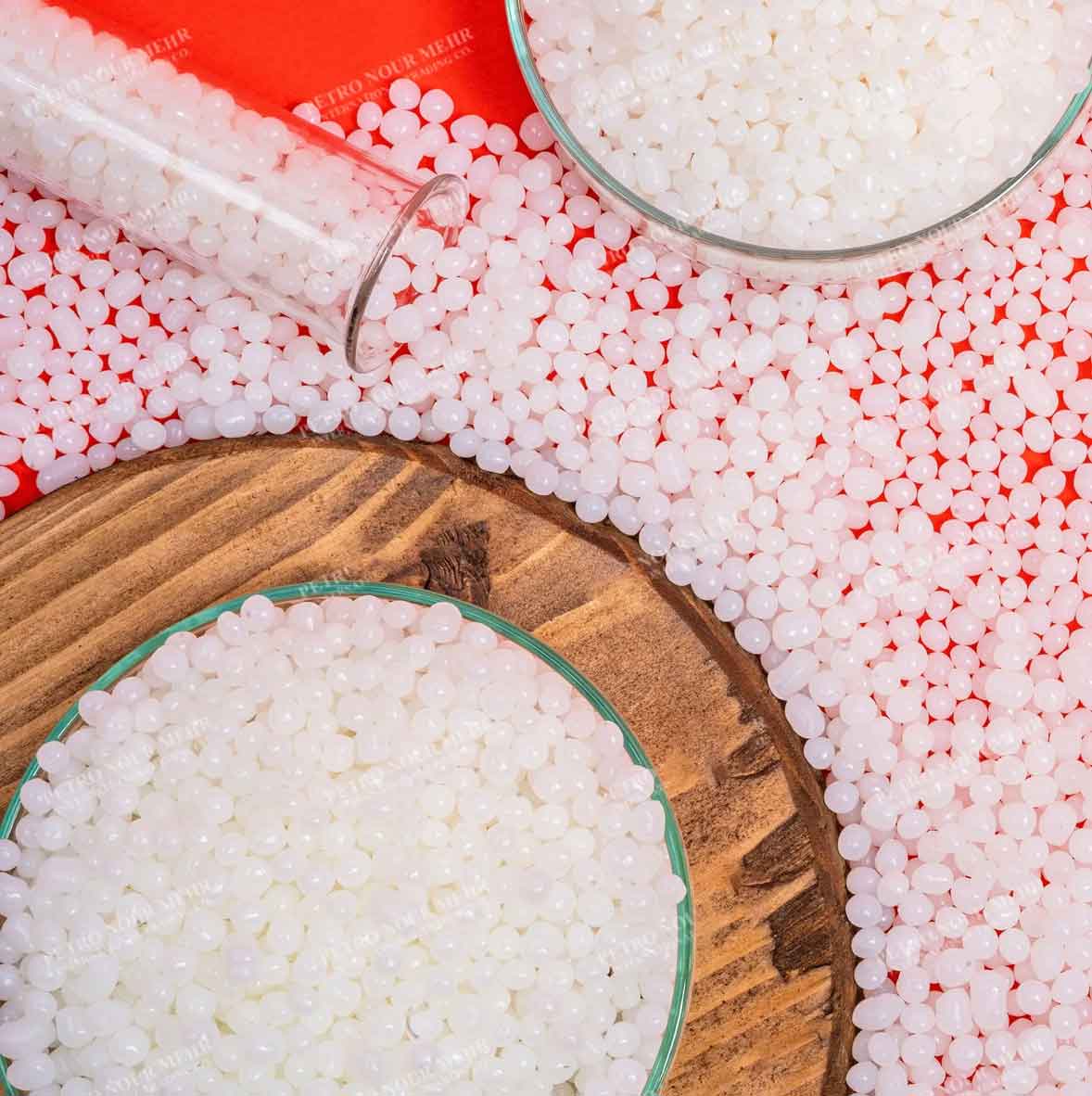
PBR Manufacturers in Iran
In the petrochemical industry of Iran, several companies and production units are engaged in the production of PBR. These companies include:
- Shazand Arak Petrochemical Company
- Takhte-jamshid Petrochemical Company
These units are among the largest PBR producers in Iran and play a significant role in supplying domestic needs and exporting this material to global markets.
PBR Manufacturers Worldwide
Despite various challenges such as changes in global markets and constraints related to raw materials, polymer and rubber manufacturers strive to meet increasing global demand by employing advanced technologies and optimizing production processes. This growth underscores the greater importance of this industry in various sectors including automotive, packaging, construction, and electronics, playing a significant role in the global economy.
Across the globe, some major producers of polybutadiene rubber (PBR) include:
- Petroquimica de Venezuela, S.A: Located in Venezuela, this petrochemical company is one of the major PBR producers in the Americas. They specialize in producing a variety of polymer products including PBR.
- Fox River Associates, LLC: Based in the United States, this company manufactures various types of polybutadiene rubber suitable for different applications such as industrial and consumer rubber goods.
These producers are just a few examples of companies active in the production of PBR worldwide. There are numerous other companies involved in this industry, producing different types of this polymer material for various applications.
Applications of PBR
Polybutadiene rubber (PBR) finds numerous applications across various industries due to its unique properties and versatility. Some common applications of polybutadiene rubber include:
- Tire Manufacturing: PBR is extensively used in tire manufacturing, both in passenger vehicle tires and commercial vehicle tires. It is particularly valued for its excellent abrasion resistance, low rolling resistance (which improves fuel efficiency), and good grip characteristics.
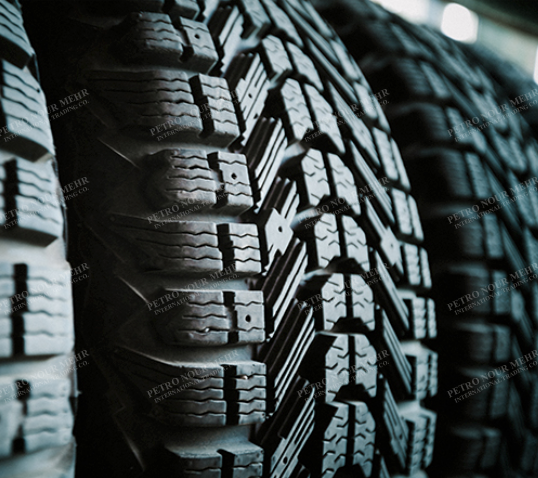
- Industrial Rubber Products: PBR is used in various industrial rubber products where durability, resilience, and flexibility are required. This includes conveyor belts, hoses, seals, gaskets, and vibration dampers.
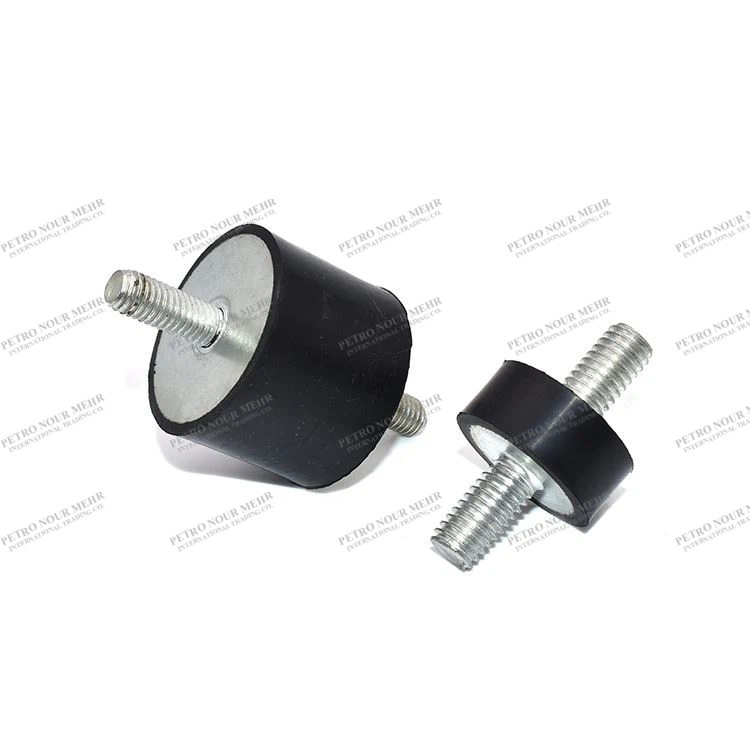
- Footwear: PBR is used in the production of shoe soles and heels due to its wear resistance, flexibility, and comfort properties. It helps in providing cushioning and grip in footwear applications.
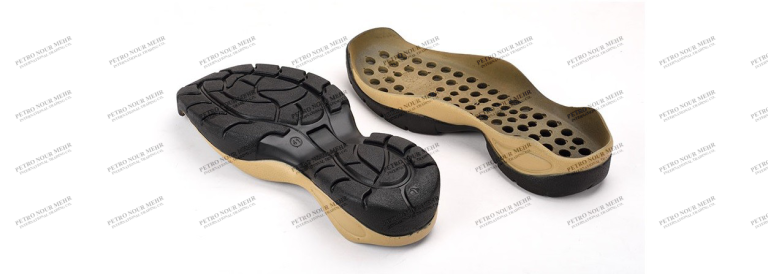
- Automotive Components: Apart from tires, PBR is used in automotive components such as automotive mounts, bushings, and anti-vibration parts. Its resilience and resistance to wear make it suitable for these applications.
- Construction Industry: PBR is used in construction for seals and gaskets in building materials, waterproof membranes, and as an additive in asphalt to improve its properties.
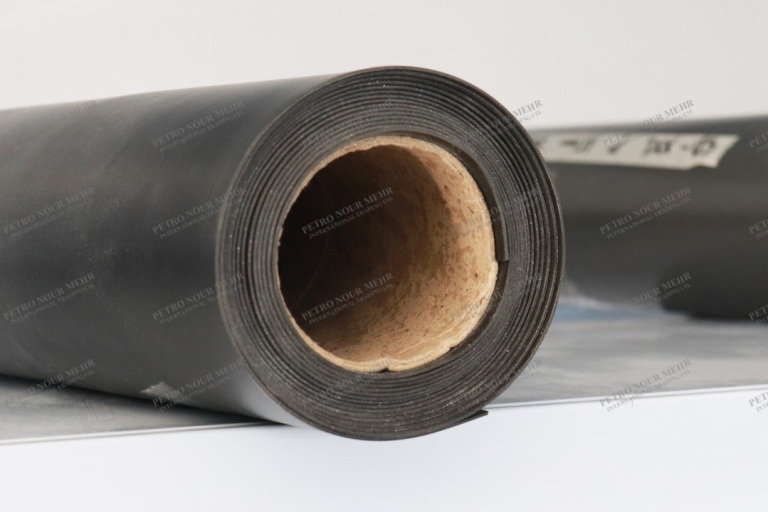
- Packaging: PBR is utilized in packaging applications where flexibility, toughness, and resistance to environmental factors are required. It helps in enhancing the durability and performance of packaging materials.
- Electronics: In electronics, PBR is used in wire and cable insulation due to its electrical insulating properties and resistance to environmental stresses.
- Adhesives and Sealants: PBR is sometimes used as an additive in adhesives and sealants to improve their flexibility, adhesion, and durability.
Overall, the diverse applications of polybutadiene rubber stem from its excellent mechanical properties, chemical resistance, resilience, and ability to withstand a wide range of temperatures and environmental conditions. These properties make PBR a preferred material in many critical industries worldwide.
Storage Conditions for PBR
This polymer material can be stored under various conditions, but there are some guidelines for better preservation of their quality:
- It is best to store these materials in a cool and dry environment, with the optimal storage temperature being below 20 .
- Protect the material from direct sunlight and UV light, as these lights can cause changes in its physical and chemical properties.
- Polybutadiene rubber react with certain chemicals such as solvents and acids. Therefore, it is better to avoid direct contact with these types of materials.
- Make sure the material has protection from impacts and scratches while being stored and transported, since physical harm may cause modifications to its mechanical and structural characteristics.
- The packaging of these materials should be made of suitable materials that protect against environmental changes and prevent water and moisture penetration into the packaging.
- For some specific products, special storage conditions may be required. In this case, refer to the manufacturer’s guidelines.
Packaging for Polybutadiene rubber
For packaging and exporting solid polybutadiene rubber (PBR), various methods can be utilized depending on environmental conditions, product requirements, and transportation facilitation for export. Below are some common methods for packaging and exporting this polymer material:
- Packaging in Small Bags: In this method, the rubber is packed into smaller bags with a capacity of about 20 to 25 kilograms.
- Wooden Box Packaging: This is a common method for packaging PBR, where the rubber is packed inside large wooden boxes with varying capacities (typically between 500 to 2000 kilograms). These boxes provide protection against contamination and moisture, making them suitable for road, sea, and air transportation.
- Use of Pallets: PBR is usually packed on large pallets for transportation purposes.
Adherence to international packaging standards, labeling requirements, and transportation conditions can significantly impact the choice of suitable packaging and export methods for PBR. It is also crucial to ensure protection of the product against shocks, moisture, and environmental damage during transportation.
Advantages and Disadvantages of PBR
Polybutadiene rubber (PBR) offers numerous advantages that make it a desirable choice for various applications across different industries. These advantages include water resistance, tear resistance, flex fatigue resistance, ozone resistance, abrasion resistance, sunlight resistance, flexibility at low temperatures, resilience to pressure, tear propagation resistance, gas impermeability, impact resistance, cut growth resistance, resistance to alcohols, vegetable and animal oils, acids, bases, and oxidation. However, it also comes with several drawbacks such as thermal resistance, lack of ignition delay, low resistance to oils and gasoline, undesirable receptivity, and low resistance to ozone.
Because of these characteristics, careful consideration of both the advantages and disadvantages is necessary when selecting and using this type of rubber.
One of the significant advantages of polybutadiene rubber is its high tear resistance, making it an ideal choice for applications requiring high mechanical strength. Additionally, it performs well at temperatures as low as -60 , making it very useful for applications in cold conditions. Furthermore, the ability to use PBR as an additive to enhance the strength and mechanical properties of other rubbers is another advantage of this material.
Despite its advantages, PBR has certain drawbacks. One major drawback is its sensitivity to heat. This rubber may melt at high temperatures, which makes it unsuitable for applications requiring high heat resistance. Additionally, its low processability can slow down production processes, ultimately leading to increased production costs. Lastly, its sensitivity to oxygen can lead to oxidation and changes in its properties, which is another significant drawback.
In conclusion, while PBR offers substantial benefits, its limitations must be carefully considered to ensure it is suitable for the intended application.
Physical and Chemical properties of PBR:
Polybutadiene rubber (PBR) is widely used in many industries such as automotive, industrial rubber, packaging, and construction due to its properties such as flexibility, abrasion resistance, and oxidation resistance. This type of rubber is a popular choice in various industrial and commercial applications due to its relatively low production cost and desirable characteristics. The physical and chemical properties of PBR are as follows:
- Flexibility and High Tensile Strength: PBR exhibits high flexibility and excellent tensile strength, making it suitable for products that require flexibility and expansion.
- Abrasion and Wear Resistance: PBR has good resistance to abrasion and wear, which makes it a key component in the production of industrial rubbers.
- Heat Resistance: PBR shows good heat resistance and can operate effectively at different temperatures without significant changes in its properties.
- Chemical Resistance: PBR demonstrates good stability against chemical agents such as oxygen, acids, and bases, making it suitable for diverse applications in chemical environments.
- Compatibility and Mixing: PBR can easily be mixed with other polymer materials and various chemicals, allowing it to be used effectively in production processes and blending applications.
These properties highlight why PBR is favored in industrial and commercial applications where durability, flexibility, and chemical resistance are essential requirements.
Types of PBR grades:
Polybutadiene rubber (PBR) is typically classified into different types based on its microstructure and properties. The main types of polybutadiene rubber include:
- High cis-PBR: This type of PBR has a high percentage of cis-1,4 structure (around 98% or higher). High cis-PBR exhibits excellent elasticity, resilience, and low temperature flexibility. It is commonly used in applications requiring high performance and durability, such as tire treads and industrial rubber products.
- Low cis-PBR: Low cis-PBR has a lower percentage of cis-1,4 structure compared to high cis-PBR (usually around 40-60% cis content). It tends to have slightly lower resilience and abrasion resistance but better processability and cost-effectiveness. It finds applications in automotive components, footwear, and some industrial products.
- High trans-PBR: This type of PBR has a high percentage of trans-1,4 structure (typically over 90%). High trans-PBR is known for its high tensile strength, tear resistance, and resistance to heat buildup. It is used in tire sidewalls, conveyor belts, and other applications where these properties are critical.
- Butadiene-styrene rubber (SBR): Although technically not pure polybutadiene rubber, SBR is a copolymer of butadiene and styrene. It combines the properties of both polymers, offering good abrasion resistance, flexibility, and aging stability. SBR is widely used in tire manufacturing and various industrial applications.
Each type of polybutadiene rubber is tailored to specific performance requirements, making them suitable for a wide range of applications across industries such as automotive, construction, packaging, and electronics.
How to Buy Polyethylene?
- Buy from a reputable and authorized supplier that holds necessary certifications and guarantees quality.
- Compare the prices of these materials in different markets and compare them with the global market price.
- Examine the sales conditions regarding quantity, delivery time, packaging, transportation methods, and payment terms.
- If you intend to import polystyrene from foreign countries, investigate customs and legal regulations and comply with export and import regulations.
- Contact bravopolymer to obtain the most suitable export price based on your conditions.
- After signing the contract, you can place your order.
- Secure and suitable payment methods according to customer preferences are provided by the company.
- Then, the loading stage is completed by selecting and introducing a transport company.
- Necessary documents for customs clearance at the destination city are also provided to customers by bravopolymer.
The largest distributor of polymers in the Middle East

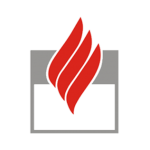

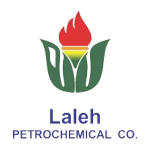
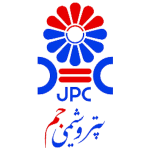
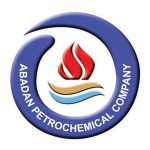
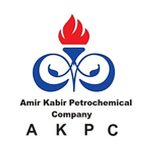
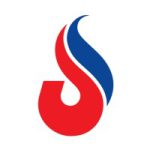
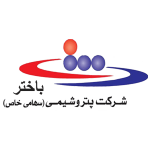
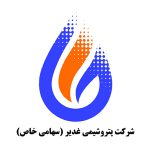
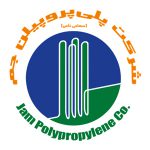
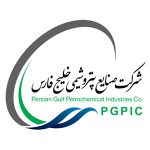
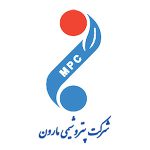
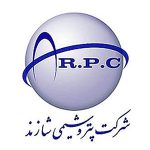
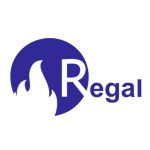
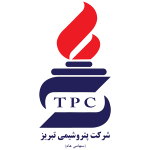
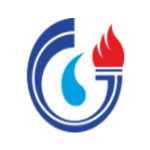